Global shortages and sharply rising costs for resources used in the textile industry, such as water, wastewater, and fossil fuels, are leading to ever-increasing pressure in the industry.
There are many ways to counteract this pressure, for example by using highly efficient dyes and auxiliaries or by optimizing processes. However, there is also a need for machine optimizations and the successes achieved by machine manufacturers in this respect allowed to reduce water consumption through low and lower liquor ratios (FV).
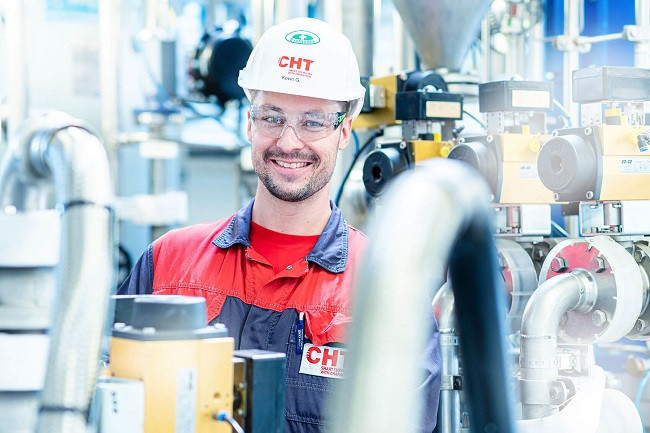
Despite all the positive aspects of this trend towards lower liquor ratios, the practical effects on the dyeing result must not be ignored and the processes must be adapted accordingly to meet the requirements, for example regarding the fastness level.
- General information on low and ultra-low liquor technology
First, it is necessary to define terminology and show which developments have been implemented and where we push the borders of physical limitations.
In contrast to the liquor ratios of earlier times, when liquor ratios ranged normally between 15:1 to around 30:1, today's usual liquor ratios have been reduced to at least around 8:1 to 12:1. Consequently, liquor ratios of over 12:1 are now considered high. Below this, the range between 6:1 and 8:1 is referred to as shorter liquor ratios, while liquor ratios of less than 6:1 to around 5:1 are regarded as low liquor ratios. The range below this can then be described as an ultra-low liquor. However, liquor ratios of less than 4:1 or even 3:1 is hardly achievable in reactive dyeing. An exception to this is dyeing on a jigger, where liquor ratios of 1:3 to 1:2.5 are perfectly possible, depending on the material.
The following specifically covers the challenges in reactive dyeing. In principle, the statements also apply to the dyeing of synthetic fibers of course. However, the liquor ratio has the greatest impact on this dye class, particularly due to the high water and time consumption of the rinsing process for reactive dyeing. In addition to saving water, fewer chemicals are also required for dyeing, which means that a reduced salt concentration in wastewater is also a significant advantage of short liquor technology. Shorter liquor ratios also allow the installation of smaller circulation pumps, which reduces power consumption and therefore electricity consumption. In addition, the design of the machines can be kept more compact, which means less material is used and therefore also helps to conserve resources.
It should also be mentioned that the amount of steam required to heat up dye baths is significantly reduced with smaller volumes.
- Technology and problems
A lower limit in the liquor ratio is given by the liquor retention capacity of cotton (“carry-over”). This depends on the fabric construction and is usually 200-250 % for cotton. It is therefore relatively high, especially compared to synthetic fibers. A liquor retention capacity of 250 % means that with a liquor ratio of 1:2.5, the entire liquor would be absorbed by the cotton and there would be no freely circulating liquor. Therefore, the liquor ratio for dyeing such an article must always be greater than 1:2.5. The liquor retention capacity for rinsing is at least as important as for dyeing. The lower the liquor ratio and the higher the liquor retention capacity, the less favorable the effect of a rinsing bath. This means that compared to higher liquor ratios, the number of rinsing baths must be increased to achieve the same fastness level. Although more rinsing baths are necessary, the amount of water required is reduced by the short liquor technology.
To illustrate how the liquor ratio affects the rinsing effect and the number of rinsing baths, let us look at the two practical examples.
Example 1
Test on machine type 1 with an LR of 6:1.
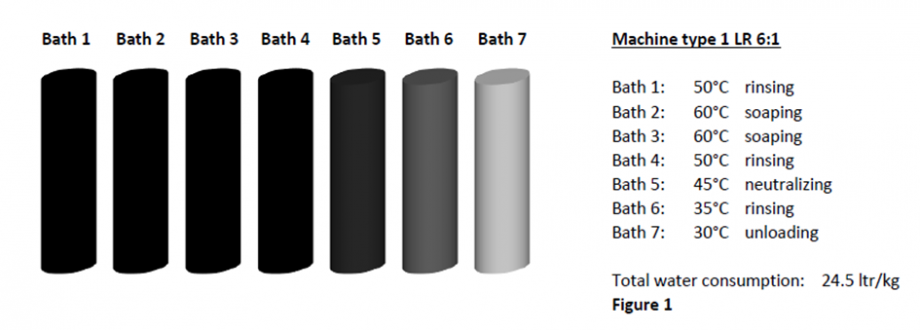
Figure 1
The black formulation used for the rinsing and washing baths in Fig. 1 was as follows.
0.45 % BEZAKTIV Red ONE
5.40 % BEZAKTIV Black ONE
Considering a liquor retention capacity of 250%, a rinse water consumption of 7 x 3.5 l/kg could be assumed for 7 baths in this case. This means that 24.5 l/kg of rinse water was used in total.
Example 2
In comparison, the second example with a longer liquor ratio shows that, despite the higher dye input, fewer baths were required to achieve approximately the same washing result, but it is obvious that the total rinse water consumption is significantly higher with the higher liquor ratio.
Test on machine type 2 with an LR of 12:1.
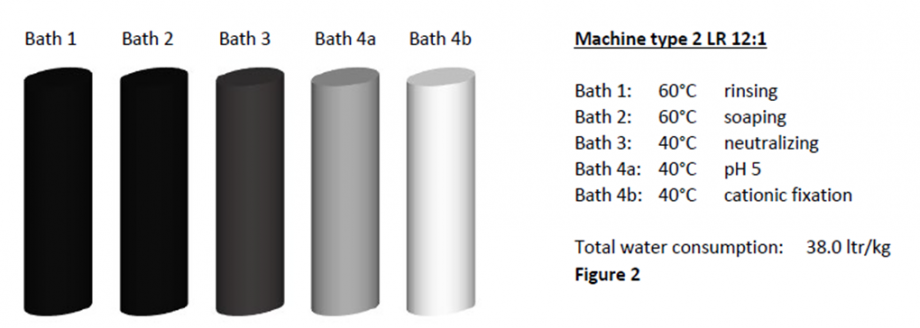
Figure 2
The rinsing and washing baths in Fig. 2 were obtained after dyeing with the following formulation:
0.55 % BEZAKTIV Orange ONE
7.65 % BEZAKTIV Black ONE
Considering a liquor retention capacity of 250%, a rinse water consumption of 4 x 9.5 l/kg could be assumed for 4 baths in this case. This means that 38 l/kg of rinse water was used here.
(Bath no. 4b is not included, as the fixation took place directly in bath 4b)
To further illustrate the influence of the liquor retention capacity, calculations for 3 different liquor ratios are shown in the following examples:
If we assume an expected liquor retention capacity of 250% for a load of 100 kg of cotton knitted fabric, this means that 2.5 liquor points, corresponding to 2.5 l/kg liquor remain in the fabric each time the bath is exchanged with a drop/fill rinse. The values shown in the following table are based on 3 rinsing bath exchanges.
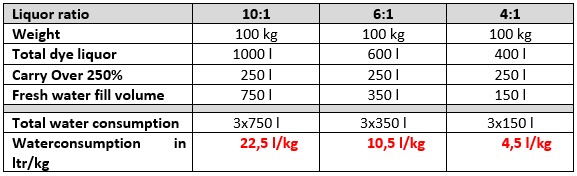
It is not yet clear from this table which fastness level is achieved after three rinses with liquor ratios 10:1, 6:1 and 4:1 and how many rinsing baths are necessary in each case to achieve the desired fastness level. In practice, several tests with different numbers of rinsing baths would have to be carried out. The BEZAKTIV Soaping Advisor can provide efficient support here. This calculation program, which is included in the CHT Textile Dyes app, enables these variants to be simulated quickly and easily by calculating the fastness grade in advance under different rinsing conditions. This allows the optimum rinsing process to be quickly determined and applied. For this calculation, the decisive parameters, namely the number and temperature of the rinsing baths as well as the liquor ratio and the liquor transfer, are considered.
If the BEZAKTIV Soaping Advisor is applied to the recipe shown in example 1, the fastness ratings after dyeing and six rinses at a liquor ratio of 6:1 is the same as dyeing at LR 6:1 and three rinsing baths at 12:1. However, at a liquor ratio of 12:1, 28 % more water is used than with 6:1.
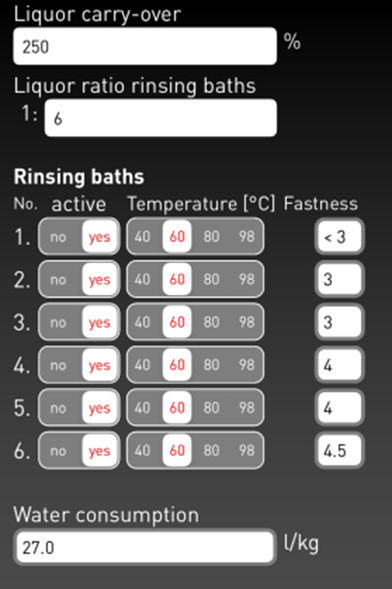
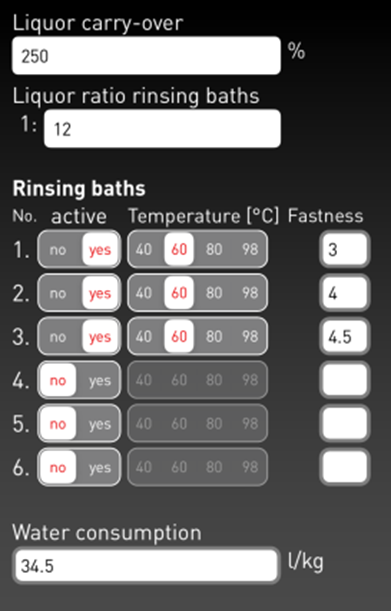
The calculated water consumption includes the water quantity for the dyeing liquor, hence the deviations from the water quantities calculated above, which only relate to the rinsing process. The BEZAKTIV Soaping Advisor is a recipe-specific guide for every dyehouse to decide whether the water savings from a short liquor ratio or the time and energy savings from a long liquor ratio offers advantages to their specific operation when rinsing.
Continuous rinsing should also be mentioned here as an alternative to total bath exchange rinsing. Almost all machine manufacturers offer systems that can shorten the rinsing process. However, more water is consumed in this process than with total bath exchange rinsing. For continuous rinsing processes, it should be considered that the available water pressure affects the amount of water used in l/min and therefore has a significant influence on the washing result. Particularly in continuous rinsing processes, a fluctuating water supply, together with fabric turnover times of >3 min, can lead to visible losses in the wash result and thus the wet fastnesses. With jet systems, the fabric turnover speed has an influence on the rinsing effectiveness due to the mechanical effect. The higher the turnover speed and thus also the number of liquor contacts, the more intensive the washing effect.
In addition to the purely energetic and ecological aspects, the adaptation of pre-treatment and dyeing recipes must also be considered. It should not be forgotten that the concentration of fats, waxes, preparations, and water hardening agents to be removed from the fabric increases subsequently to the reduction of liquor ratio.
On the one hand, this requires the use of very stable and highly effective products, but also a significant increase to the quantities used in longer liquor ratios. Depending on the effectiveness of the products used, specifying the quantities as a percentage of the fabric weight is a perfectly sensible way of achieving an “automatic” adjustment.
- Conclusions
As already mentioned in previous publications, the effectiveness of the full bath exchange is still the best option in terms of water consumption and energy requirements. Due to the wide range of machines now available, it is difficult to give a general assessment of which rinsing procedure is the right one. Therefore, in practice usually country-specific conditions are considered. If the primary goal is to save time to generate the highest possible productivity, then continuous rinsing options are used, instead of full bath exchanges!
Even today, water and energy costs are often not realistically considered in some companies, in contrast to the time factor.
Furthermore, the parameters of individual machine designs, material properties and the availability of process water, including the availability of hot water in production, should also be analyzed in detail.